The Future of EV Efficiency
Electric vehicles (EVs) are rapidly evolving, and one of the most exciting advancements in this space is the integration of battery technology into the vehicle’s structure.
The Xiaomi SU7 is leading the charge with its Cell-to-Body (CTB) technology, setting a new standard for how EVs are designed.
This innovation allows the battery to become an integral part of the vehicle’s load-bearing structure, streamlining design, reducing height, and boosting efficiency.
Cell-to-Body: A New Era of Structural Integration
Cell-to-Body technology is a game-changer in vehicle design. By integrating the battery directly into the chassis, manufacturers can eliminate traditional components like the floor pan.
The battery housing cover itself takes on structural duties, making the vehicle more compact.
For the Xiaomi SU7, this approach reduces the overall height by 17mm. A significant improvement that contributes to both aerodynamics and interior space.
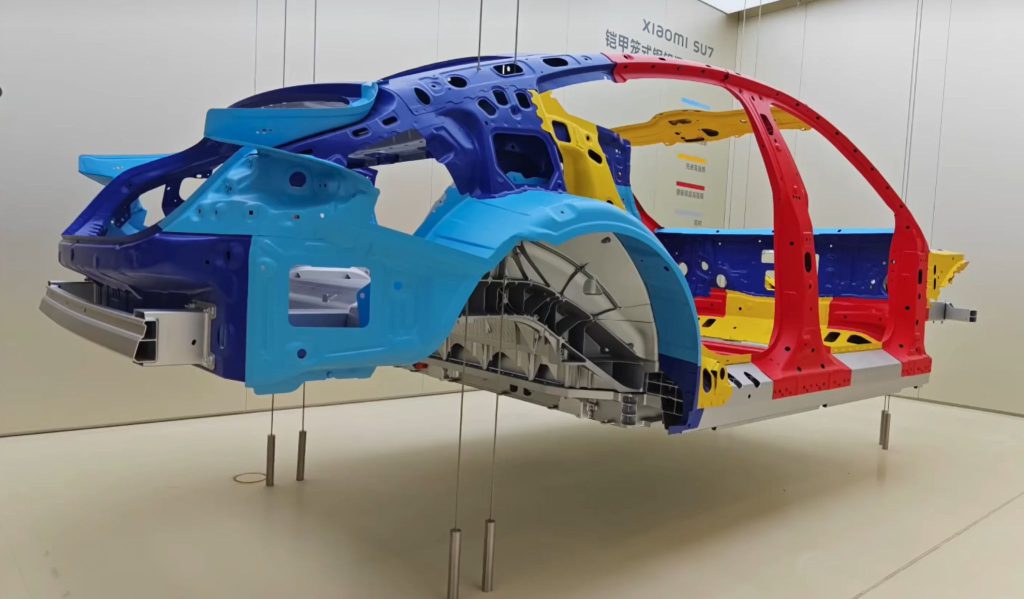
Industry Leaders Embrace Structural Batteries
Xiaomi isn’t alone in this pursuit.
Major players in the EV industry are adopting similar technologies under different names, all aiming for the same goal: maximizing efficiency through structural integration.
- BYD refers to its approach as “Cell-to-Body,” mirroring Xiaomi’s strategy. This method allows for a more streamlined vehicle architecture, contributing to a lighter, more efficient design.
- Tesla has coined the term “Cell-to-Chassis” for its approach. By integrating the battery into the chassis, Tesla enhances the vehicle’s structural integrity while also freeing up space for other components.
- Xpeng is also exploring similar technology, aiming to improve the balance between vehicle weight and battery capacity, leading to better performance and range.
- Leapmotor is leveraging this technology to push the boundaries of EV design, creating vehicles that are both more spacious and efficient.
Why Structural Integration Matters
The adoption of Cell-to-Body and similar technologies by leading EV manufacturers highlights the importance of functional integration in vehicle design. These advancements enable manufacturers to:
- Optimize Space: With the battery housing integrated into the chassis, vehicles can achieve a more compact design without compromising on interior space.
- Enhance Efficiency: By reducing the number of components and integrating the battery into the structure, vehicles become lighter, leading to improved energy efficiency and longer range.
- Improve Safety: The structural role of the battery enhances the vehicle’s overall rigidity, contributing to better crash protection and occupant safety.
- Simplify Manufacturing: Fewer components mean simpler assembly processes, reducing manufacturing costs and time.

The Competitive Edge of CTB Technology
As EV manufacturers continue to innovate, those who embrace technologies like Cell-to-Body will gain a competitive edge.
This integration not only leads to more efficient and safer vehicles but also aligns with the industry’s shift towards sustainability.
By reducing the number of materials and components. These technologies contribute to a greener manufacturing process.
The Road Ahead for EV Design
The future of electric vehicle design is clearly moving towards greater integration and efficiency.
As companies like Xiaomi, BYD, Tesla, Xpeng, and Leapmotor continue to develop and refine their structural battery technologies. We can expect to see even more innovations that push the boundaries of what EVs can achieve.
This trend is set to revolutionize the way vehicles are built, offering consumers better-performing, safer, and more efficient electric cars.
In the competitive world of electric vehicles.The integration of batteries into the structural design marks a significant milestone.
With technologies like Cell-to-Body leading the way. The industry is on the cusp of a new era in automotive design—one that prioritizes efficiency, safety, and sustainability.
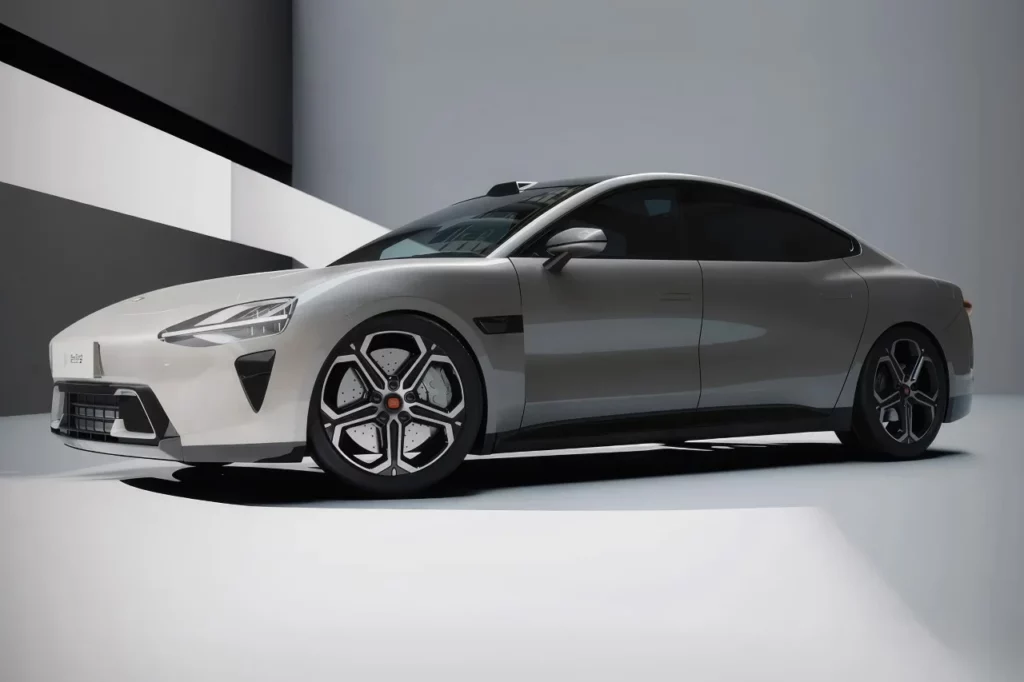
#LivingWithGravity