Introduction to the TPEM Facility in Sanand
January 12, 2024, marks a momentous occasion for Tata Motors as they celebrate the rollout of the first car from the new TPEM facility in Sanand, Gujarat. This state-of-the-art plant, sprawling across 460 acres, is set to revolutionize automotive manufacturing in India. The facility is dedicated to producing both internal combustion engine (ICE) and electric vehicle (EV) models, showcasing Tata Motors’ commitment to innovation and sustainability.
The new TPEM facility in Sanand, Gujarat, will manufacture a range of Tata Motors’ internal combustion engine (ICE) and electric vehicle (EV) models. While the specific models produced at this facility may vary over time, Tata Motors is expected to focus on both popular existing models and new upcoming releases in both the ICE and EV segments. Here are some likely candidates:
ICE Models:
- Tata Tiago
- Tata Tigor
- Tata Altroz
- Tata Nexon
EV Models:
- Tata Nexon EV
- Tata Tigor EV
- Tata Altroz EV
- Upcoming EV models (future releases)
The facility’s advanced infrastructure and high level of automation will ensure the production of high-quality vehicles, meeting the growing demand for both ICE and EV models in the Indian market. Tata Motors’ commitment to innovation and sustainability will be evident in the models produced at this cutting-edge plant.
Key Features of the TPEM Facility
Cutting-Edge Manufacturing Technology
The TPEM facility is equipped with advanced technology to ensure precision manufacturing. It houses four main shops: Stamping, Body Construction, Paint, and Final Assembly. These shops are integrated with high levels of automation and the latest technological advancements, setting new benchmarks in the industry.
High Level of Automation
Automation is at the heart of the TPEM facility’s operations. The integration of automated systems in the stamping, body construction, paint, and final assembly shops ensures a high degree of precision and efficiency. This level of automation not only enhances production speed but also ensures consistent quality across all manufactured vehicles.
Environmental and Economic Impact
Sustainable Practices
The TPEM facility incorporates several world-class technologies aimed at reducing environmental impact. From energy-efficient machinery to waste reduction practices, Tata Motors is committed to creating a sustainable manufacturing process. This commitment aligns with global trends towards greener automotive production and positions Tata Motors as a leader in sustainable manufacturing.
Economic Benefits for Gujarat
The establishment of the TPEM facility in Sanand is expected to bring significant economic benefits to the region. It will create numerous job opportunities, boost local businesses, and contribute to the overall economic development of Gujarat. The facility’s presence will also attract ancillary industries, further strengthening the local economy.
Future Prospects for Tata Motors
Expansion of EV Production
With the increasing demand for electric vehicles, the TPEM facility is poised to play a crucial role in Tata Motors’ EV strategy. The plant’s advanced infrastructure will support the production of next-generation electric vehicles, helping Tata Motors capture a larger share of the growing EV market.
Commitment to Quality and Innovation
Tata Motors’ investment in the TPEM facility underscores its commitment to quality and innovation. By leveraging cutting-edge technology and automation, Tata Motors aims to deliver superior products that meet global standards. This focus on quality and innovation will enhance Tata Motors’ competitiveness in the global automotive market.
The inauguration of the TPEM facility in Sanand, Gujarat, marks a significant milestone for Tata Motors and the Indian automotive industry. With its advanced technology, high level of automation, and commitment to sustainability, the TPEM facility is set to redefine automotive manufacturing standards. This new plant not only strengthens Tata Motors’ manufacturing capabilities but also contributes to the economic and environmental well-being of the region.
Also let us take a look at how Tata Nexon EV is made in the same plant.
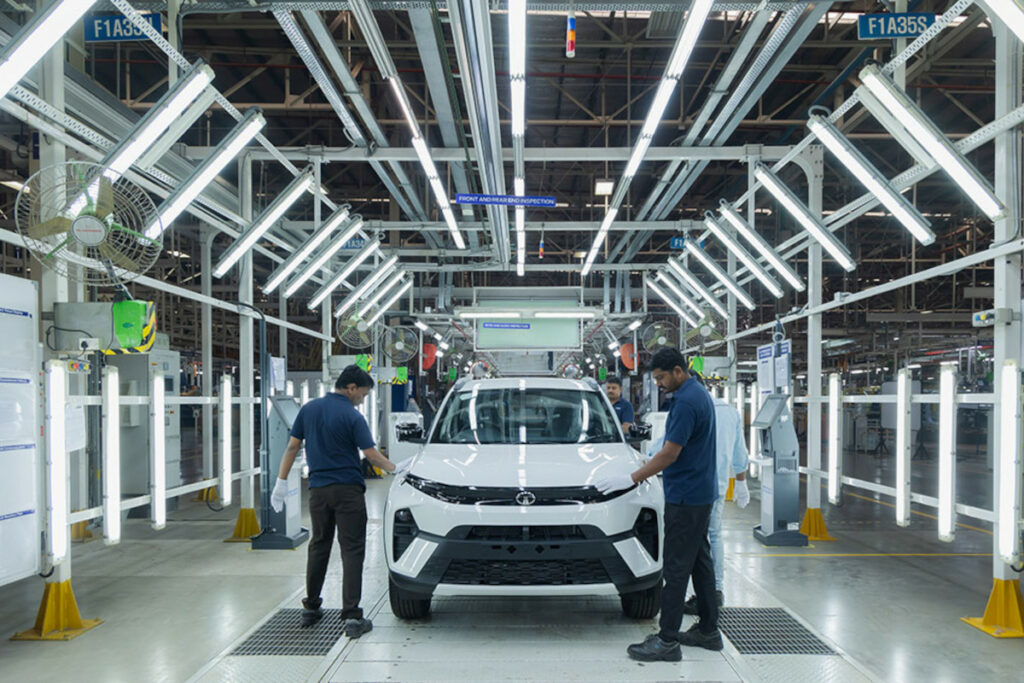
How the Tata Nexon EV is Made: A Comprehensive Overview
Introduction The Tata Nexon EV, one of Tata Motors’ flagship electric vehicles, is manufactured with precision and advanced technology. The process encompasses several stages, from stamping and body construction to painting, final assembly, and rigorous quality checks. Here’s a detailed look at how the Tata Nexon EV is made at the new TPEM facility in Sanand, Gujarat.
1. Stamping Shop
Raw Material Processing
- High-strength steel sheets are procured and prepared for stamping.
- The sheets are cut into appropriate sizes using automated cutting machines.
Stamping Process
- The cut steel sheets are fed into stamping presses.
- The stamping presses, equipped with dies, shape the sheets into various car body parts such as doors, hoods, and fenders.
- The process involves multiple stages to achieve the final shape with precise dimensions.
2. Body Construction Shop
Body Assembly
- Stamped parts are transferred to the body construction shop.
- Robots and automated systems assemble the parts, welding them together to form the car’s body structure.
- High-precision robotic welders ensure strong and accurate welds.
Inspection and Quality Checks
- Each welded assembly undergoes stringent quality checks to ensure structural integrity and dimensional accuracy.
- Automated inspection systems and human inspectors work together to detect any defects.
3. Paint Shop
Pre-treatment
- The assembled car bodies are cleaned and treated to remove impurities and prepare the surface for painting.
- This process includes degreasing, phosphating, and rinsing.
Painting Process
- The car bodies are coated with primer to enhance adhesion and corrosion resistance.
- Electrostatic painting techniques are used to apply the base coat and clear coat, ensuring uniform coverage and high-quality finish.
- The painted bodies are baked in ovens to cure the paint, ensuring durability and a glossy finish.
4. Final Assembly Shop
Component Installation
- The painted car bodies are moved to the final assembly line.
- Major components such as the electric motor, battery pack, suspension, and braking systems are installed.
- Interior components, including seats, dashboard, and infotainment systems, are also fitted.
Electrical Systems Integration
- The car’s electrical systems, including wiring harnesses and electronic control units (ECUs), are integrated.
- Software and firmware are uploaded to the car’s control systems to ensure proper functioning.
5. Quality Assurance and Testing
Functional Tests
- The assembled Tata Nexon EV undergoes a series of functional tests to ensure all systems are operating correctly.
- This includes testing the electric drivetrain, braking system, lights, and other electronic components.
Road Testing
- Each vehicle is subjected to road tests to evaluate performance, handling, and ride quality.
- This step ensures the Nexon EV meets Tata Motors’ standards for safety and driving experience.
Final Inspection
- A comprehensive final inspection is conducted to verify the car’s overall quality.
- Any minor defects or issues are addressed before the vehicle is approved for delivery.
Conclusion
The manufacturing process of the Tata Nexon EV at the TPEM facility in Sanand, Gujarat, exemplifies Tata Motors’ commitment to quality, innovation, and sustainability. The use of advanced technology and automation ensures that each Nexon EV is built to the highest standards, ready to meet the demands of modern consumers.
By focusing on precision manufacturing and rigorous quality checks, Tata Motors continues to lead the way in the electric vehicle market, delivering reliable and efficient vehicles like the Tata Nexon EV.